Project
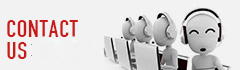
Contact person: Zhang Xingqian 13912340688
Phone: 0519-81182602
Fax: 0519-81182602
whatsapp:+8618961131360
Website: glgresearch.com.cn
Email: yz@yzdryer.com steven@yzdryer.com
Special production line for magnesium fluorosilicate flash drying machine



Special production line for magnesium fluorosilicate flash drying machine
Description
The XSG series rotary flash drying machine is a new type of drying equipment developed by our factory on the basis of introducing and absorbing foreign technology. This machine has innovative technology, reasonable design, compact structure, wide application range, large production capacity, good product quality, high efficiency, energy saving, and can be dried, crushed, and screened in one device at a time to eliminate environmental pollution. The overall performance of the machine has reached the international technical level.
Hot air enters the mixing and crushing drying chamber from the bottom of the dryer at an appropriate spraying speed through the inlet pipe, exerting strong shearing, blowing, and rotating effects on the material. As a result, the material is subjected to centrifugation, shearing, collision, and friction, and is divided into particles, enhancing mass and heat transfer. At the bottom of the dryer, larger and wetter particle clusters are mechanically crushed under the action of the agitator, while particles with lower moisture content and smaller particle size are carried up by the rotating airflow and further dried during the upward process. Due to the rotational flow between gas and solid phases, the inertia of the solid phase is greater than that of the gas phase, and the relative velocity between the solid and gas phases is higher, which enhances the mass and heat transfer between the two phases. Therefore, the production intensity of this machine is high.
Multiple feeding devices are available for selection, ensuring continuous and stable feeding without any bridging during the process.
A special cooling device is installed at the bottom of the dryer to prevent the material from deteriorating in the high-temperature zone at the bottom.
Special air pressure sealing devices and bearing cooling devices effectively extend the service life of the transmission part.
The special air distribution device reduces equipment resistance and effectively provides the processing air volume of the dryer.
The drying room is equipped with a grading ring and a swirl plate, and the material fineness and final moisture content can be adjusted. (If the final water content of calcium carbonate can be adjusted to ≤ 0.1%)
Compared to other drying methods, it can effectively increase the specific gravity of materials.
The drying chamber has a high circumferential gas velocity and short material retention time, effectively preventing material adhesion and thermal sensitive material deterioration, achieving efficient, fast, small equipment, and large-scale production.
Inorganic materials: Boric acid, calcium carbonate, hydroxide, copper sulfate, iron oxide, barium carbonate, antimony trioxide, various metal hydroxides, various heavy metal salts, synthetic cryolite, etc.
Organic compounds: atrazine (pesticide insecticide), lauric acid, benzoic acid, benzoic acid, fungicide, sodium oxalate, cellulose acetate, etc.
Ceramics: kaolin, silica, clay.
Dyes: anthraquinone, black iron oxide, indigo pigment, butyric acid, titanium hydroxide, zinc sulfide, various intermediate azo dyes.
Food category: soy protein, gelatinous starch, distiller's grains, wheat sugar, and wheat starch.
model | Host internal management (mm) | Processing air volume (m3/h) | Evaporative water volume (kg/h) | Large installed capacity (KW) | Large height (m) | Occupy the plane (m2) |
XSG-4 | 400 | 1150-2300 | 58-73 | 21.4 | 4.6 | 27 |
XSG-6 | 600 | 2500-5100 | 130-163 | 34.2 | 5.5 | 39 |
XSG-8 | 800 | 4500-9000 | 238-297 | 63.5 | 6.0 | 40 |
XSG-10 | 1000 | 7000-13500 | 345-430 | 68 | 6.5 | 55 |
XSG-12 | 1200 | 10000-20000 | 515-645 | 94 | 6.8 | 62 |
XSG-14 | 1400 | 16600-28000 | 730-910 | 130 | 7.0 | 89 |
XSG-16 | 1600 | 18000-38100 | 962-1203 | 160 | 7.2 | 160 |
Note:
1. The evaporation of water is calculated based on an inlet temperature of 200 ℃ and an outlet temperature of 80 ℃
2. The installed capacity is the basic data and can be changed according to the material performance.
3. The land area is arranged according to the actual situation, and the data in the table is for reference only.