Category
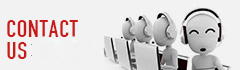
Contact person: Zhang Xingqian 13912340688
Phone: 0519-81182602
Fax: 0519-81182602
whatsapp:+8618961131360
Website: glgresearch.com.cn
Email: yz@yzdryer.com steven@yzdryer.com
FL series boiling granulator dryer (one-step granulator)



FL series boiling granulator dryer (one-step granulator)
Description
Granulation in the pharmaceutical industry: tablet granules, granule granules, capsule granules.
Granulation in the food industry: cocoa, coffee, milk powder, granular juice, seasoning, etc
Granulation in other industries: pesticides, feed, fertilizers, pigments, dye chemicals, etc.
Drying of wet materials in powder or granular form.
Coating: granules, pill protective layer, color preparation, sustained release, film, enteric coating, etc
The material powder particles are in an annular fluidized state in the raw material container (fluidized bed). They are preheated and mixed by purified heated air, and the adhesive solution is atomized and sprayed in, causing several particles to aggregate into agglomerates containing the adhesive. Due to the continuous drying of the material by hot air, the moisture in the agglomerates evaporates, and the adhesive solidifies. This process is repeated continuously, forming ideal and uniform microporous spherical particles.
● Improve flowability and reduce dust flying through powder granulation:
● Improve its solubility through powder granulation;
Mixing, granulation, and drying are completed in one machine for one-step granulation;
● Using anti-static filter cloth for safe equipment operation;
● Set pressure relief holes to prevent equipment and personnel from being injured in the event of an explosion;
The equipment has no dead corners, and loading and unloading materials are light and fast. It is washed clean and meets GMP standards.
project | unit | model | |||||||||
3 | 5 | 15 | 30 | 60 | 120 | 200 | 300 | 500 | |||
Raw material container | capacity | L | 12 | 22 | 45 | 100 | 220 | 420 | 670 | 1000 | 1500 |
diameter | mm | 300 | 400 | 550 | 700 | 1000 | 1200 | 1400 | 1600 | 1800 | |
production capacity | small | Kg | 1.5 | 4 | 10 | 15 | 30 | 80 | 100 | 150 | 250 |
big | Kg | 4.5 | 6 | 20 | 45 | 90 | 160 | 300 | 450 | 750 | |
fan | fan | m3/h | 1000 | 1200 | 1400 | 1800 | 3000 | 4500 | 6000 | 7000 | 8000 |
wind presssure | mmH2O | 375 | 375 | 480 | 480 | 950 | 950 | 950 | 950 | 950 | |
power | Kw | 3 | 4 | 5.5 | 7.5 | 11 | 18.5 | 22 | 30 | 45 | |
steam consumption | Kg/h | 15 | 23 | 42 | 70 | 141 | 211 | 282 | 366 | 451 | |
Compressed air consumption | m3/min | 0.9 | 0.9 | 0.9 | 0.9 | 1.0 | 1.0 | 1.1 | 1.5 | 1.5 | |
main engine weight | Kg | 500 | 700 | 900 | 1000 | 1100 | 1300 | 1500 | 1800 | 2000 | |
steam pressure | Mpa | 0.3~0.6 | |||||||||
temperature | ℃ | Adjustable within the range of room temperature -120 ℃ | |||||||||
task time | min | Depending on material characteristics 45-90 | |||||||||
Material yield rate | ﹪ | ≥99 | |||||||||
noise | dB(A) | Isolation installation between fan and host, noise ≤ 75 dB (A) | |||||||||
External dimensions of the host L × W × H | m | 1.0×0.6 ×2.1 | 1.2×0.7 ×2.1 | 1.25×0.9 ×2.5 | 1.6×1.1 ×2.5 | 1.85×1.4 ×3 | 2.2×1.65 ×3.3 | 2.34×1.7 ×3.8 | 2.8×2.0 ×4.0 | 3×2.25 ×4.4 |